1.
Dépôt chimique en phase vapeur (CVD): Les gaz sources de carbone généralement utilisés sont des hydrocarbures tels que l'éthylène et le méthane, tandis que des catalyseurs métalliques tels que le fer, le nickel, le cobalt, etc. sont généralement choisis pour le catalyseur. Le substrat à déposer (par exemple, une plaquette de silicium, une plaquette de verre, etc.) est placé dans une chambre de réaction pour s'assurer que la surface du substrat est propre et plane. La chambre de réaction est chauffée à une température appropriée, puis aspirée à un certain niveau de vide afin de garantir la pureté et la stabilité des gaz pendant le processus de réaction. Le gaz source de carbone et le gaz catalyseur sont introduits dans la chambre de réaction par l'intermédiaire d'un système d'alimentation en gaz permettant de contrôler le débit et le volume du gaz. Le gaz source de carbone se dissocie à la surface du catalyseur pour générer des atomes de carbone, qui se déposent ensuite à la surface du substrat pour former des nanotubes de carbone. Le temps de croissance des nanotubes de carbone est contrôlé, généralement de quelques minutes à quelques heures, afin de contrôler la longueur et la densité des nanotubes. Une croissance prolongée permet d'obtenir des nanotubes de carbone plus longs et plus denses. À la fin de la croissance, l'alimentation en source de carbone et en gaz catalyseur est interrompue et la chambre de réaction est refroidie à la température ambiante. À la fin de la réaction, le gaz résiduel dans la chambre de réaction est éliminé par l'apport d'un gaz inerte tel que l'azote ou l'argon.
2. Méthode d'enrobage : La suspension de nanotubes de carbone est déposée sur la surface du substrat par spin-coating, pulvérisation, brossage ou laminage. Au cours du processus d'enduction, des paramètres tels que la vitesse d'enduction et la vitesse de rotation de la tête d'enduction peuvent être contrôlés pour maîtriser l'épaisseur et l'uniformité du film. Après l'enduction, le revêtement est placé dans une zone ventilée ou sur un banc chauffé pour induire l'évaporation du solvant. Une fois le solvant complètement évaporé, le séchage est effectué pour former un film uniforme de nanotubes de carbone. Le film de nanotubes de carbone est éventuellement soumis à un traitement thermique afin d'en améliorer la cristallinité et les propriétés mécaniques. Les conditions de traitement thermique peuvent être ajustées en fonction des besoins et sont généralement réalisées sous atmosphère de gaz inerte.
3. Filtration : Les matériaux couramment utilisés pour les membranes filtrantes sont le polycarbonate (PC), le polyester (PET) et le polyamide (Nylon). La taille des pores est généralement choisie en fonction de l'épaisseur du film et de la perméabilité souhaitées. La suspension de nanotubes de carbone est filtrée sur la membrane filtrante sous vide ou sous pression. Les opérations de filtration peuvent être effectuées à l'aide d'équipements tels que des entonnoirs de filtration sous vide ou des filtres à membrane.
4. Méthode de décapage : les méthodes de décapage courantes comprennent le décapage mécanique, où le film de nanotubes de carbone est directement décollé du substrat à l'aide d'outils de décapage (par exemple, rubans, grattoirs, etc.), ) ; le décapage chimique, qui consiste à placer le film de nanotubes de carbone cultivé dans un solvant ou une solution appropriés de manière à endommager la liaison entre le film et le substrat pour réaliser le décapage ; et le décapage thermique, qui consiste à chauffer le substrat ou le film pour le dilater ou le contracter thermiquement afin de détruire la liaison entre le substrat et le film pour réaliser le décapage ; et le décapage thermique, qui consiste à chauffer le substrat ou le film pour le dilater ou le contracter thermiquement afin de détruire la liaison entre le substrat et le film pour réaliser le décapage. Le décapage thermique consiste à chauffer le substrat ou le film pour le faire se dilater ou se contracter thermiquement, ce qui permet de rompre le lien entre le substrat et le film.
5.3.3 Étude de cas : Membranes d'osmose inverse renforcées par des nanotubes de carbone
Les membranes d'osmose inverse constituent une application unique des nanotubes de carbone, en plus d'applications fonctionnelles similaires à d'autres types de membranes de filtration. Cette technologie de séparation par membrane est capable de séparer les impuretés, les ions, les micro-organismes, etc. de l'eau, ce qui est largement utilisé dans les domaines de l'eau potable, du traitement des eaux usées industrielles et du dessalement de l'eau de mer. Cependant, la membrane d'osmose inverse présente le problème d'un faible flux et d'une faible efficacité de traitement. Pour résoudre ce problème, les chercheurs ont introduit des nanotubes de carbone dans les membranes d'osmose inverse. Les nanotubes de carbone possèdent d'excellentes propriétés telles qu'une surface spécifique élevée, une grande résistance, une conductivité élevée, etc., qui peuvent former une sorte de canal conducteur de protons dans la membrane d'osmose inverse et augmenter le flux. En même temps, les nanotubes de carbone peuvent également adsorber les ions, les micro-organismes et d'autres impuretés dans l'eau, ce qui peut améliorer efficacement l'efficacité de la purification de l'eau et la durée de vie de la membrane d'osmose inverse. À l'heure actuelle, la membrane d'osmose inverse à base de nanotubes de carbone a été mise en service commercial, dans le domaine de l'eau potable, du dessalement de l'eau de mer et dans d'autres domaines, et a obtenu des résultats significatifs. À l'avenir, la recherche et la technologie de préparation des matériaux à base de nanotubes de carbone seront encore développées, et le flux et l'efficacité de traitement des membranes d'osmose inverse seront continuellement améliorés.
Tableau 2 Comparaison des propriétés des nanotubes de TiO2, du GO et des NTC
Propriétés
|
Membranes à nanotubes de dioxyde de titane (TiO2)
|
Membranes en oxyde de graphène (GO)
|
Membranes en nanotubes de carbone (CNT)
|
Structure du matériau
|
Nanotubes d'oxyde de titane
|
Oxyde de graphène avec groupes fonctionnels contenant de l'oxygène
|
Nanotubes de carbone
|
Méthode de préparation
|
Méthode de mise en solution Méthode de dépôt en phase vapeur Méthode électrochimique
|
Méthode de revêtement Méthode de dépôt chimique en phase vapeur Méthode hydrothermique
|
Dépôt chimique en phase vapeur Méthode de revêtement Méthode de filtration
|
Domaines d'application
|
Photocatalyse Dispositifs photovoltaïques Purification de l'eau et de l'air
|
Traitement de l'eau Purification de l'air Séparation moléculaire Biomédecine
|
Traitement de l'eau Membranes d'osmose inverse Séparation moléculaire Biomédecine
|
Avantages de la photocatalyse
|
Grande surface Propriétés photovoltaïques spéciales Activité photocatalytique
|
Nombreux groupes fonctionnels contenant de l'oxygène Activité de surface élevée Sélectivité moléculaire
|
Résistance élevée Conductivité élevée Surface spécifique élevée Performance ajustable
|
Inconvénients
|
Processus de préparation complexe et coût élevé
|
Susceptible de présenter des défauts structurels et une mauvaise stabilité au cours du processus de préparation
|
Processus de préparation complexe Exigences élevées en matière de contrôle des processus
|
Applications
|
Traitement photocatalytique de l'eau Purification de l'air Préparation de dispositifs photovoltaïques
|
Traitement de l'eau Séparation moléculaire Applications biomédicales
|
Membranes d'osmose inverse Séparation moléculaire Applications biomédicales
|
6 Membranes à base de cadres métallo-organiques (MOF)
6.1 Qu'est-ce qu'une membrane MOF ?
La
structure métallo-organique (MOF) est un polymère de coordination fabriqué par auto-assemblage de ligands organiques polydentés contenant de l'oxygène, de l'azote, etc. avec des ions de métaux de transition. Il se compose de centres métalliques inorganiques et de ligands organiques pontants reliés par auto-assemblage pour former un matériau poreux cristallin avec une structure de réseau périodique. En tant que matériau hybride organique-inorganique, le MOF possède à la fois la rigidité des matériaux inorganiques et la flexibilité des matériaux organiques.
Les structures de type dorsal dans différentes dimensions sont principalement déterminées par la coordination entre les ligands organiques et les ions métalliques ainsi que par la liaison hydrogène. Au cours du processus de synthèse, les réactifs résiduels et les petites molécules de solvants occupent les pores de la structure du squelette, tandis que l'élimination des petites molécules par traitement d'activation peut laisser une structure de pores persistante. La taille et la structure des pores peuvent être modifiées en changeant la structure des ligands organiques et le type d'ions métalliques dans la matière première synthétisée afin de contrôler la surface spécifique et la porosité en fonction des différentes applications. Actuellement, les matériaux à squelette métallo-organique utilisés avec des ligands organiques neutres hétérocycliques contenant de l'azote ou avec des ligands organiques anioniques contenant du carboxyle peuvent être synthétisés en grandes quantités, ce qui présente un grand potentiel de développement et d'application dans la recherche sur les matériaux modernes.
6.2 Comment produire des membranes MOF ?
1. Méthode de synthèse in situ : en fonction des propriétés de surface particulières du support lui-même, celui-ci est directement placé dans le système de synthèse et, dans certaines conditions, la surface du support et la nuit de formation du film entrent directement en contact et réagissent pour préparer une membrane continue. La méthode de synthèse in situ est simple et facile à mettre en œuvre, facile à produire à grande échelle, mais il est difficile de préparer une membrane MOF continue, car les propriétés chimiques entre les matériaux MOF et les supports sont plus différentes, le taux de nucléation des cristaux est réduit, ce qui entraîne une faible densité de nucléation hétérogène des cristaux MOF sur la surface du support, et une mauvaise liaison entre la membrane et le support.
2. Méthode de croissance secondaire du germe de cristal : on utilise d'abord la méthode hydrothermique pour faire croître le germe de cristal sur le substrat, puis, après le processus de nucléation des cristaux, la croissance de la couche de la membrane, la croissance secondaire du matériau pour obtenir une membrane dense. Enfin, les espèces cristallines de la surface du substrat poreux après une température élevée, la réaction de condensation entre les groupes et les grains de zéolithe se combinent pour former des liaisons covalentes. Toutefois, cette méthode est quelque peu limitée car la membrane filtrante ne résiste pas à des températures élevées.
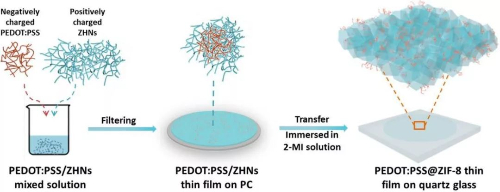
Fig. 10 Synthèse schématique d'un film MOF : Film PSS@ZIF-8
6.3 Application spécialisée dans l'élimination des métaux lourds
Outre les applications fonctionnelles similaires à d'autres types de membranes de filtration, les membranes MOF peuvent être utilisées pour le traitement des ions de métaux lourds. Les membranes MOF ont une structure poreuse très ordonnée formée par des ions métalliques et des ligands organiques par liaison chimique. Cette structure poreuse a un diamètre et une taille de pore réglables, offrant de nombreux sites et canaux d'adsorption, qui sont favorables à l'adsorption et à l'intégration des ions de métaux lourds. Cela permet d'utiliser les films MOF dans le domaine du traitement de l'eau, notamment pour éliminer les polluants à base d'ions de métaux lourds, tels que le plomb, le cadmium et le mercure, des eaux souterraines, des eaux usées industrielles et des eaux usées municipales. La taille des pores et la fonctionnalisation de la surface des films MOF, très contrôlables, permettent une adsorption efficace et une séparation sélective des ions de métaux lourds spécifiques. Ils jouent également un rôle dans le traitement par adsorption et la récupération pour l'assainissement de l'environnement et les processus de traitement des eaux usées. Les films MOF peuvent capturer et récupérer efficacement les métaux cibles lors de l'adsorption des ions de métaux lourds. Grâce à des méthodes de post-traitement appropriées, les ions de métaux lourds adsorbés peuvent être désorbés du film MOF, ce qui permet de récupérer et de réutiliser efficacement les ressources métalliques.
7 Membrane filtrante composite
Les membranes filtrantes composites sont différentes des membranes filtrantes traditionnelles à matériau unique, car elles combinent deux matériaux ou plus pour exploiter pleinement leurs forces respectives et compenser leurs faiblesses respectives, ce qui permet d'obtenir une filtration plus efficace et plus fiable. Ces matériaux peuvent être des polymères, des céramiques, des métaux, des nanomatériaux, etc. Chaque matériau possède des propriétés physiques, chimiques et mécaniques uniques et peut être combiné de manière flexible en fonction des différentes exigences de filtration.
Dans les batteries lithium-ion, une membrane composite PVDF-MOF avec une couche continue de MOF sert de diaphragme haute performance. La structure poreuse uniforme et les canaux sub-nanométriques avec des sites métalliques ouverts connectés dans la couche MOF continue peuvent générer un flux Li+ uniformément réparti, inhiber la formation de protubérances dendritiques et améliorer les performances électrochimiques.
Fig. 11 Séparateur composite PVDF-MOF avec couche continue de MOF [5]
Dans le domaine du dessalement de l'eau de mer, la distillation membranaire (MD) est apparue comme une stratégie alternative de dessalement de l'eau de mer qui permet de réduire considérablement les coûts d'investissement et la consommation d'énergie. Dans le processus de distillation membranaire, presque 100 % des éléments non volatils sont éliminés et il n'y a pas de limite à la concentration de l'eau d'alimentation, alors que le processus d'osmose inverse (OI) sous pression a moins de potentiel pour traiter les solutions à forte salinité avec une faible récupération d'eau. Les composants volatils sont séparés du mélange d'alimentation à l'aide d'une membrane hydrophobe microporeuse, et le système fonctionne en dessous du point d'ébullition du liquide d'alimentation. Pour les applications MD, les matériaux polymères à faible énergie de surface, à haute stabilité thermique, chimique et inerte sont souvent préférés. Le polytétrafluoroéthylène (PTFE) et le fluorure de polyvinylidène (PVDF) sont considérés comme les principaux matériaux de membrane disponibles dans le commerce pour la distillation à membrane sous vide (DMV) en raison de leur grande stabilité thermique et de leur hydrophobie. Le PVDF et le PTFE sont les polymères optimaux pour les applications de distillation sur membrane sous vide en raison de leur excellente résistance chimique et de leur durabilité. Ces propriétés permettent au PVDF de résister aux environnements chimiques agressifs souvent rencontrés dans les systèmes VMD, garantissant ainsi une fiabilité opérationnelle à long terme. Le PTFE, quant à lui, joue un rôle clé grâce à ses propriétés antiadhésives et à son excellente résistance aux températures élevées. Dans les systèmes VMD, le PTFE contribue à améliorer les performances des membranes et empêche efficacement l'encrassement, garantissant ainsi un transport efficace et sans obstacle des vapeurs à travers la membrane pendant la distillation. Dans les applications VMD, l'utilisation synergique du PVDF et du PTFE améliore la durabilité, la résistance chimique et l'efficacité opérationnelle de l'ensemble du système membranaire.
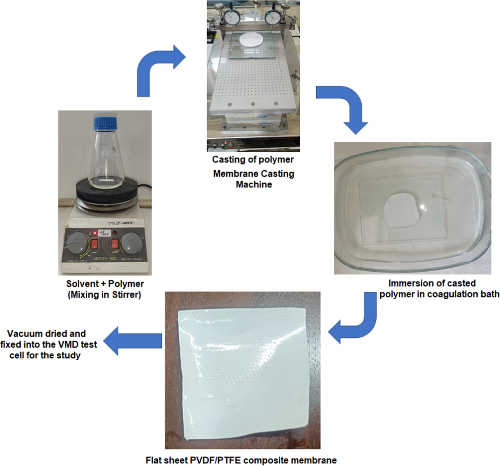
Fig. 12 Organigramme de préparation de la membrane composite microporeuse PVDF-PTFE [6]
8 Conclusion
Les membranes filtrantes composées de différents matériaux sont utilisées dans différents domaines en raison de leurs différentes caractéristiques et peuvent être sélectionnées en fonction de différents besoins en plus du processus de filtration de base. Les membranes en PVDF peuvent être utilisées pour filtrer les micro-organismes tels que les bactéries, et peuvent également être utilisées pour la purification des matériaux dans la production chimique ; les membranes en céramique sont principalement utilisées dans l'industrie alimentaire pour la séparation des boissons alcoolisées ; les membranes en nanotubes de dioxyde de titane peuvent être utilisées pour des applications connexes et pour le traitement des ions de métaux lourds en raison de leurs propriétés photocatalytiques ; les membranes en oxyde de graphène peuvent être utilisées pour la séparation moléculaire, ainsi que pour le dessalement de l'eau de mer et la séparation du pétrole et de l'eau ; les nanotubes de carbone peuvent être utilisés comme membranes d'osmose inverse ; et les membranes MOF peuvent être utilisées pour séparer sélectivement les ions de métaux lourds en raison de la nature des composés de coordination. En outre, selon les besoins des différents scénarios d'application, différents types de membranes de filtration peuvent être utilisés conjointement, et le type de membrane composite peut obtenir un meilleur effet de filtration en complétant les caractéristiques de différents types de membranes de filtration matérielles.
Stanford Advanced Materials (SAM) peut non seulement fournir une large gamme de membranes de filtration, mais aussi des conseils professionnels en matière de sélection, que vous pouvez
consulter immédiatement.
Lire aussi :
Références :
[1] Khayet M ,Feng C ,Khulbe K , et al. Preparation and characterization of polyvinylidene fluoride hollow fiber membranes for ultrafiltration[J]. Polymer,2002,43(14).
[Li M ,Cheng S ,Zhang J , et al. Poly(vinylidene fluoride)-based composite membranes with continuous metal-organic framework layer for high-performance separators of lithium-ion batteries[J]. Chemical Engineering Journal,2024,487.
[3] Hu W ,Zhang F ,Tan X , et al. Antibacterial PVDF Coral-Like Hierarchical Structure Hierarchical Structure Fabrication Film for Self-Cleaning and Radiative Cooling Effect [J]. ACS applied materials & interfaces,2024.
[4] Wei Y ,Li K ,Li P , et al. Enhanced ceramic membranes filtration by PS pre-Oxidation with CuO assisted FeSO4 catalytic for NOM removal in drinking water treatment [J]. Separation and Purification Technology,2024,345.
[5] Membranes céramiques et leurs applications dans le traitement des aliments et des boissons [J]. Filtration and Separation,2000,37(3).
[6] Mala M M ,S. S ,S. Sea and brackish water desalination through a novel PVDF-PTFE composite hydrophobic membrane by vacuum membrane distillation [J]. Discover Chemical Engineering,2024,4(1).